1-3 Regular Fiber Composites
1-3 Regular Fiber Composites
Smart Material manufactures 1-3 composites using piezo ceramic fibers as active rods. 1-3 fiber piezo composites are prepared by epoxy infiltration of fibers. This patented method is also called Arrange & Fill. Regular fiber distribution is achieved by arranging the fibers with fixed spacing.
1-3 Regular Fiber A&F Composite
- Frequencies 80kHz to 1MHz
- PZT Navy type II
- Fill Factors 15% to 48%
- Maximun dimensions 10cm by 10cm, larger on request
- Various epoxy and polyurethane interstitial materials available.
- Operational temperatures up to 135℃
- Available with Gold, Copper-Tin and Silver electrodes
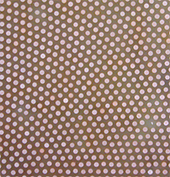
1-3 Regular Fiber Composites
Smart Material manufactures 1-3 composites using piezo ceramic fibers as active rods. PZT fiber composites are a cost-effective alternative compared to the Dice & Fill method. 1-3 fiber piezo composites are prepared by epoxy infiltration of fiber bundles and dicing of the cube-shaped blocks perpendicular to the direction of the fibers. This method is also called Arrange & Fill.
Regular pixel distribution is achieved by arranging ceramic fibers with 800µm diameter with a constant pitch. This yields fill factors of approx. 15% to a maximum of 48%.
The 1-3 fiber regular composite material was especially designed for SONAR and other underwater ultrasound applications. A modified vacuum deposition method allows for a low impedance copper-flash tin layer with a typical thickness of 2.5µm for high durability and improved solderability.
1-3 Regular Fibre Composite product spectification and selections
Resonance Frequencies | 80kHZ up to 1MHz |
|
||||||||||||||||||||||||||||||||||||||||||||||||||||||||||
Fill Factors | 15% up to 48% |
|
||||||||||||||||||||||||||||||||||||||||||||||||||||||||||
PZT Materials | PZT Navy Type II |
|
||||||||||||||||||||||||||||||||||||||||||||||||||||||||||
Acoustic Impedance | 5 MRayl to 16 MRayl |
|
||||||||||||||||||||||||||||||||||||||||||||||||||||||||||
Available Electrodes | CuSn (Copper with Tin flash layer) | |||||||||||||||||||||||||||||||||||||||||||||||||||||||||||
Dimensions | Max. 100mm by 100mm,various round diameters |
|
||||||||||||||||||||||||||||||||||||||||||||||||||||||||||
Coupling Coefficient kt | 0.61 to 0.68 | |||||||||||||||||||||||||||||||||||||||||||||||||||||||||||
Operational Temperatures | Typical 95°C, 135°C on request | |||||||||||||||||||||||||||||||||||||||||||||||||||||||||||
Interstitial Materials | Various Epoxy systems |
Typical Ultrasound Applications for 1-3 Regular Fiber Composites
- SONAR, array transducer
- SONAR, single element transducer
- General Underwater Ultrasound Applications
- Air Ultrasound Transducers
Due to the Arrange & Fill production method the raw 1-3 fiber composite material are typical blocks of up to 10cm length and the lateral dimensions of the targeted element. It also allows to machine 1-3 composites into various shapes and forms, in addition to slicing elements with the desired esonance frequency of the raw fiber block.
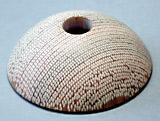
This includes precise concave or convex contours for superior broadband ultrasound receiver applications. The Arrange & Fill production method is easily scalable for volume quantities which also allows for short lead time - a major advantage over the commonly used Dice & Fill methods, especially for low frequency applications.
Smart Material offers various standard Epoxy and Polyurethane systems as the interstitial material for its random fiber composites, often called filler. The various available filler materials allow for operational temperatures between 95°C and 135°C.